Neil Forrest
Porøs

PORØS associates ideas about architecture, craft and landscape, reasoned in the form of a grotto. It works as a collection of cisterns that distribute, filter and atomize water, while soluble chemicals evaporate and deposit crystalline formations on porous ceramic forms. The project originated with a question about material porosity and how to engineer active geological and chemical processes as a kind of derelict factory or obdurate garden. Porøs is a metamorphism of science and ethnography in as geo-physical landscape.

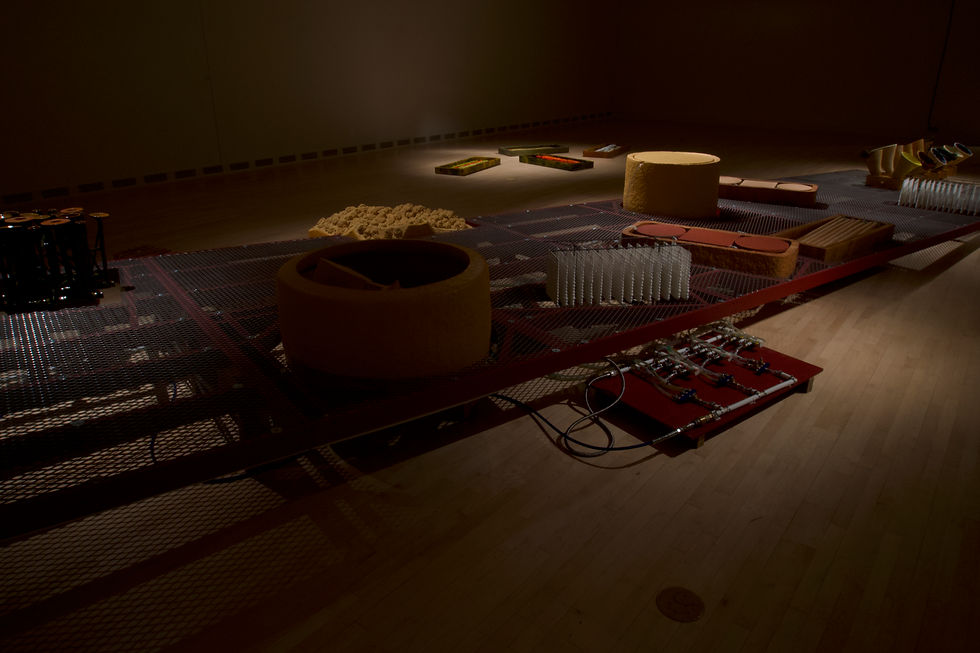
With mechanical augmentation, the cisterns distribute, filter, irrigate, and evaporate water, and some that hold representations of buildings. Water-soluble chemicals evaporate and deposit crystalline formations.
The controlled air-water mix is pushed through the ceramic pores and produce an audible atomization with a microclimate at the surface of the tablets. Combined, a geo-physical landscape is at work.
A compressed air unit (off-stage) and integrated with a water pump, are used as a control system to create an atomizing condition at the ceramic surface, producing effervescence and airborne mist.
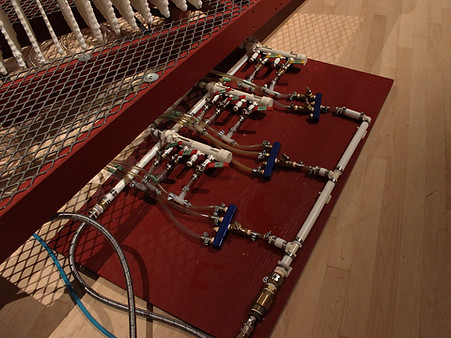


Long rods of porous ceramic (above) and tablet shapes (below), are formed with internal networks of both large and microscopic pores to distribute an air/water mixture to the surface, creating atomization and high-pitched sounds. Liquid is a narrative commodity, with fluids moving passively and pressure, and from one state to another – liquid to vapour, liquid to solid, and inititate miniature climatic events.


Two cisterns host emblematic buildings: one medieval and the other modern, both memorable destinations when I lived in Norway. These works of culture bookend the historical arc of the country in which I began the project.
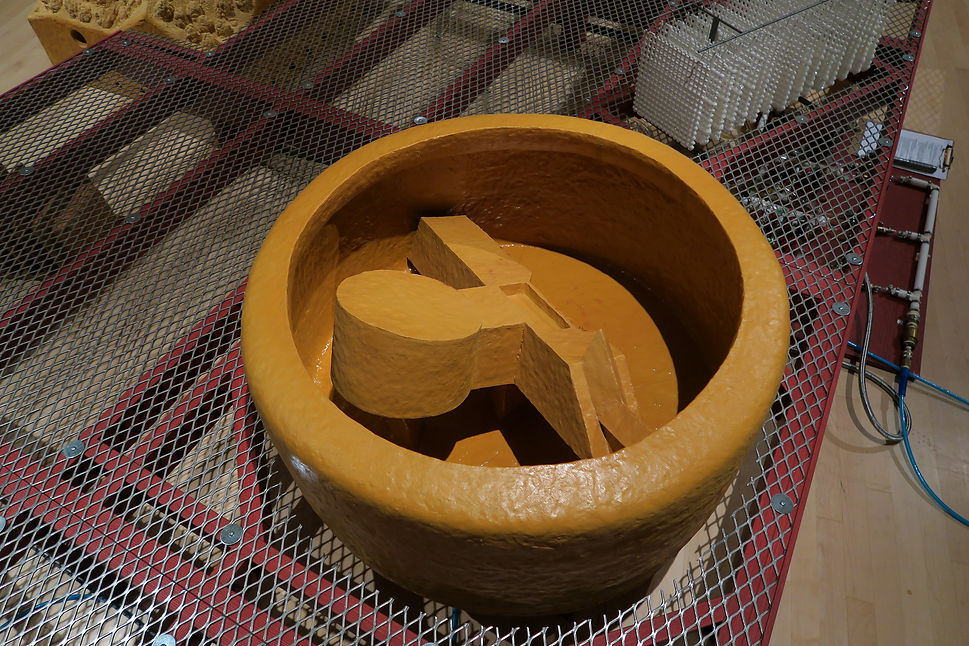
Porøs is akin to basements, underground cisterns, trenches, ship interiors and bunkers. The installation is a tilted plane with objects visible under the steel mesh of the floor, with objects and plumbing underneath. Some fluids move passively and some by pressure…an idea to see the phenomena of moving from one state to another: liquid to vapour and liquid to solid.
The datum or titled plane, is to be walked and climbed for inspection of the various objects cut into the mesh.
Above, CNC manufactured porcelain ‘mesh tiles’ are gridded to support the cultivation of crystals as part of the library of crystalline growth systems...in this case, in the shape of a file cabinet.
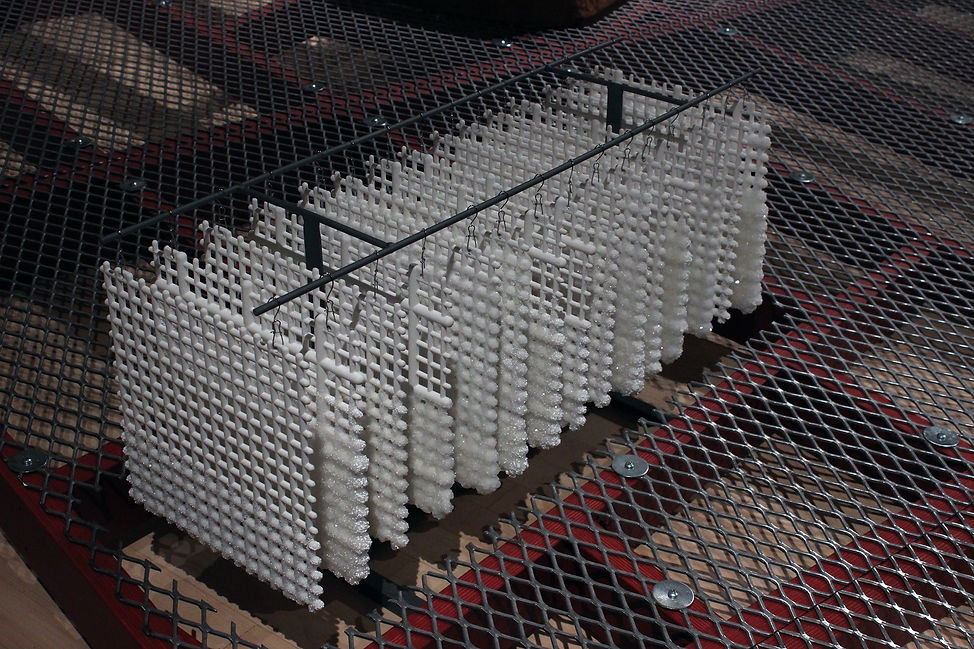
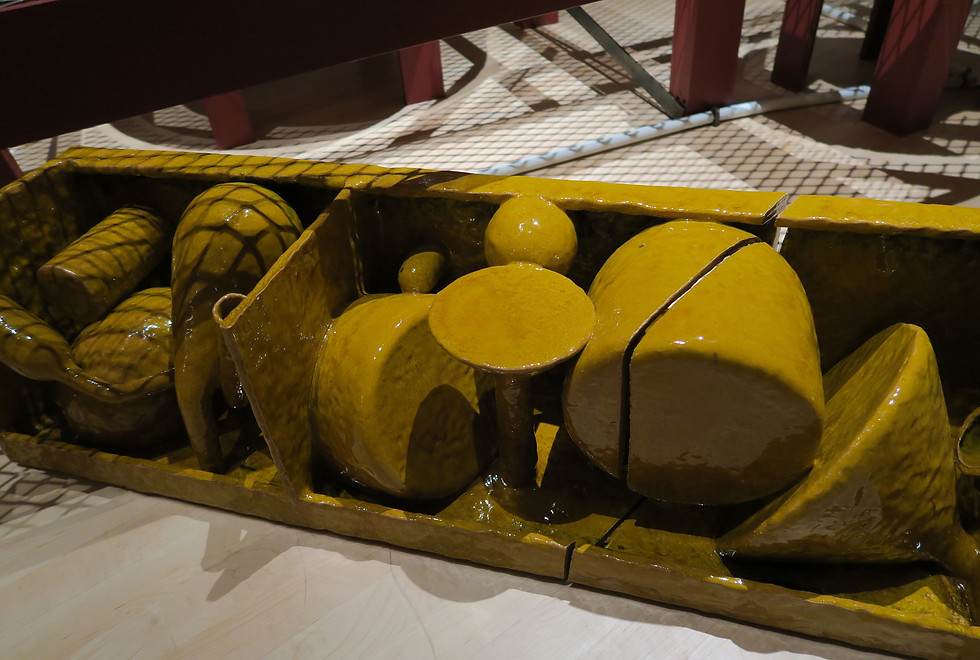
Aggregations of pressure-sprayed layers of clay develop naturalized porous forms.


Part of the landscape is made using industrial spray techniques over hollow clay shapes , which gradually disappear and transform under layers of clay particulate.



Solubles evaporate and deposit crystals on the surface of porous clay rods


Porøs follows the tradition of grottos, inspired by Bernard Palissy’s grotto for Catherine de’ Medici in Tuileries...whose emulation of Eden included four man-made rivers that represented primordial creation as both scientific as mystical.

PORØS
2015-17
stoneware & porcelain ceramics, solubles, wood, water pump, compressor, steel mesh, additional materials
handbuilt and CNC milled ceramics
Installation dimensions
14 m l x 11 m w. x 1.6 m h
45’ l x 35’ w x 5’ h
Porøs exhibited at the Nelson Fine Arts Center
ASU Art Museum, AZ
2017-18
Porøs was made possible by a generous grant from NARP, the Norwegian Artistic Research Program (Programme for kunstnerisk utviklingsarbeid)
with thanks to Jørn Mortensen, grant development
architectural system developed with Peter Henry, architect
Sam Fresia, atomizing system engineering.
Sophie Jaillet, crystal & chemistry research.
Julian Covey, crystal production
Jordan McDonald, clay materials research.
Kaas Ghanie, clay fabrication support.
Paul Firth, millwork.
Knut Natvik, kiln operations, Oslo.
© 2022 by Neil Forrest
photography by Dean Reynolds, Garth Johnson, Neil Forrest